Ottimizzare la produzione nelle aziende metalmeccaniche
Monitoraggio della produzione, riduzione dei tempi di attrezzaggio, dei fermi macchina e dei consumi energetici.
Ottimizzare la produzione nelle aziende metalmeccaniche
Monitoraggio della produzione, riduzione dei tempi di attrezzaggio, dei fermi macchina e dei consumi energetici.
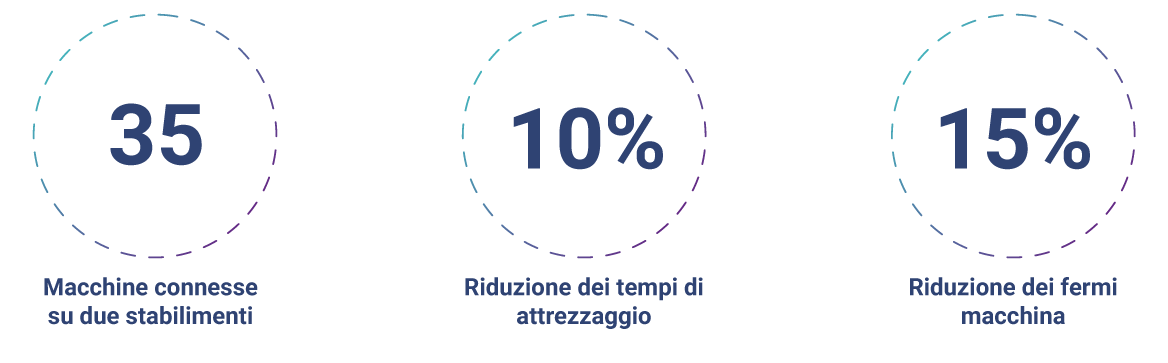
Le Sfide
Poter disporre dei dati in tempo reale relativi al funzionamento dei propri macchinari industriali risulta fondamentale per le aziende per garantire un monitoraggio attento dei consumi dell’intero processo produttivo all’interno degli stabilimenti industriali.
Un caso interessante è quello di un’azienda metalmeccanica toscana che, per far fronte a queste necessità, si è rivolta al team di Zerynth in cerca di un sistema innovativo che garantisse una maggiore fruibilità dei dati prelevati dalle macchine dei suoi impianti.
L’esigenza, infatti, era quella di monitorare l’avanzamento della produzione, quantificare le ore di funzionamento della macchina e il relativo consumo energetico così da migliorare l’efficienza del processo e ottenere una migliore integrazione tra i dati macchina e il gestionale già presente in azienda. L’interconnessione tra tutti i macchinari nello stabilimento, inoltre, era fondamentale per garantire un’adeguata comunicazione di macchine di tipologie differenti su due stabilimenti.
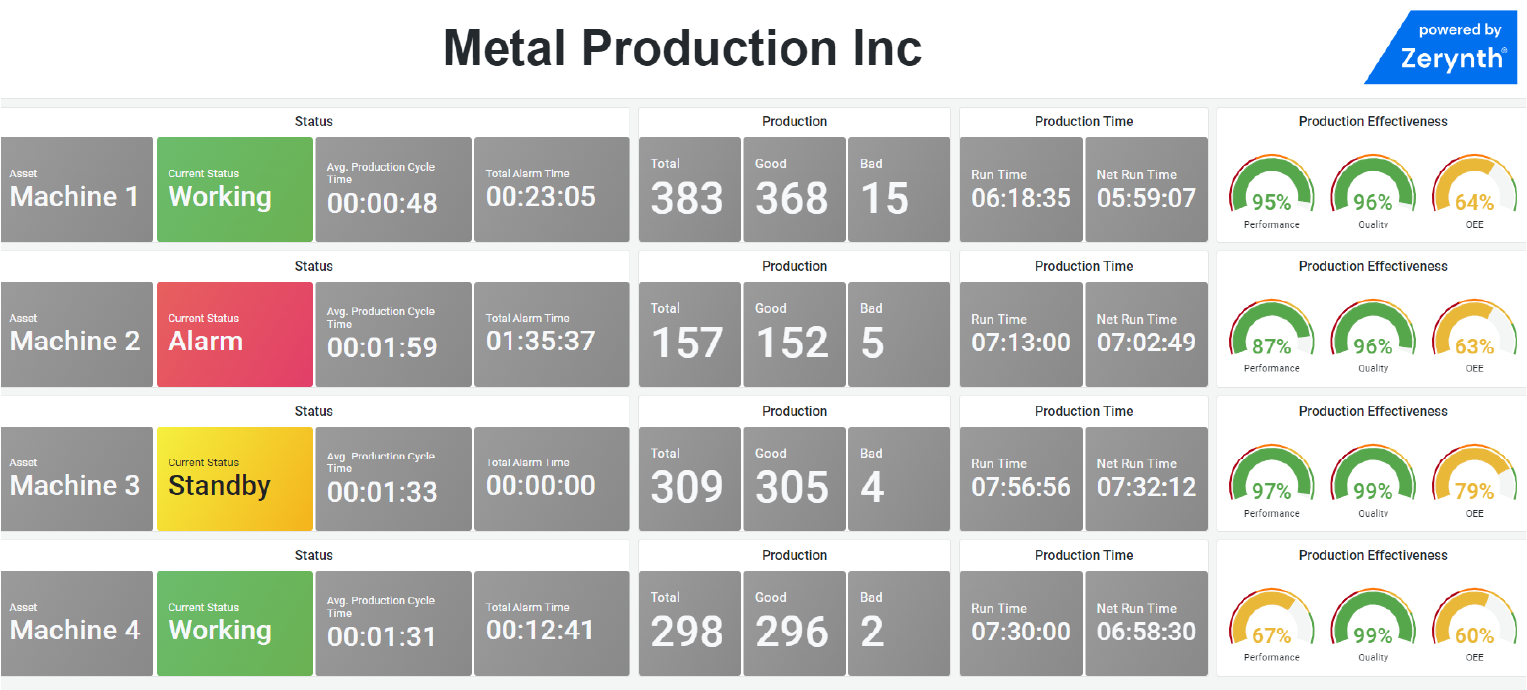
La Soluzione
La Zerynth IoT Platform è stata installata su ciascun macchinario presente nello stabilimento. Il parco macchine dell’azienda era composto da 35 macchinari sia di tipologia brownfield che greenfield, per cui è stato possibile estrarre i dati in retrofitting, attraverso il collegamento di una pinza amperometrica con ciascun edge device utilizzato. Tramite il valore di corrente, viene stimato il consumo energetico della macchina, da cui poi vengono derivate le ore di lavoro totali.
Avere a disposizione un sistema digitalizzato di monitoraggio dei macchinari, utilizzati per le lavorazioni meccaniche, ha permesso di rilevare processi non ottimizzati e di effettuare cambiamenti strategici per una riduzione dei tempi di attrezzaggio dei macchinari stessi.
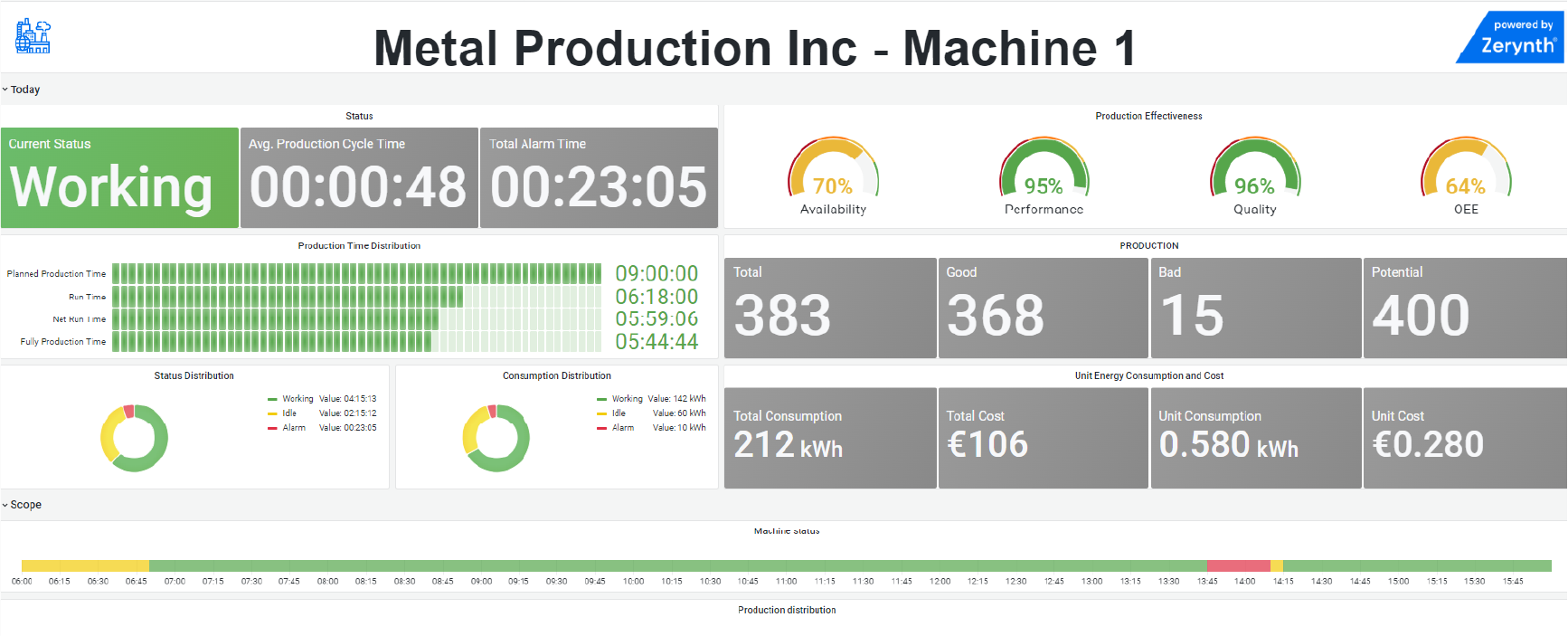
Scarica il case study per scoprire in che modo è ora possibile per l’azienda individuare le anomalie in modo immediato, ridurre sensibilmente i tempi di fermo macchina ed ottenere un’ottimizzazione completa del processo produttivo.
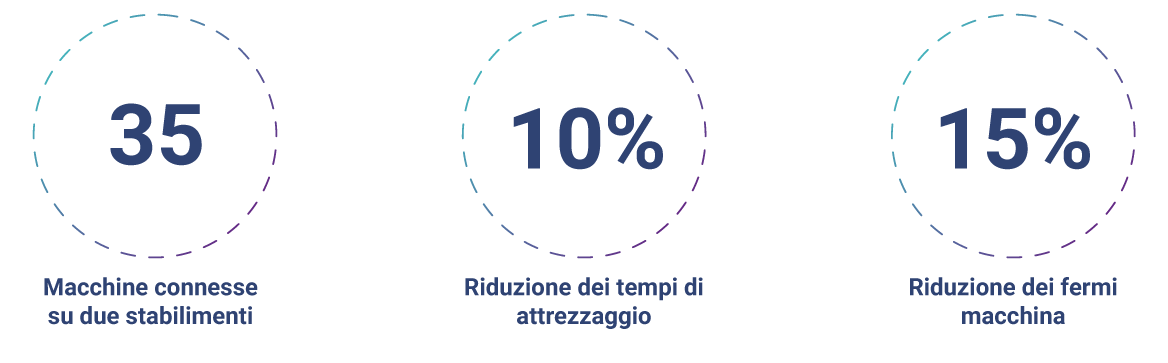
Le Sfide
Poter disporre dei dati in tempo reale relativi al funzionamento dei propri macchinari industriali risulta fondamentale per le aziende per garantire un monitoraggio attento dei consumi dell’intero processo produttivo all’interno degli stabilimenti industriali.
Un caso interessante è quello di un’azienda metalmeccanica toscana che, per far fronte a queste necessità, si è rivolta al team di Zerynth in cerca di un sistema innovativo che garantisse una maggiore fruibilità dei dati prelevati dalle macchine dei suoi impianti.
L’esigenza, infatti, era quella di monitorare l’avanzamento della produzione, quantificare le ore di funzionamento della macchina e il relativo consumo energetico così da migliorare l’efficienza del processo e ottenere una migliore integrazione tra i dati macchina e il gestionale già presente in azienda. L’interconnessione tra tutti i macchinari nello stabilimento, inoltre, era fondamentale per garantire un’adeguata comunicazione di macchine di tipologie differenti su due stabilimenti.
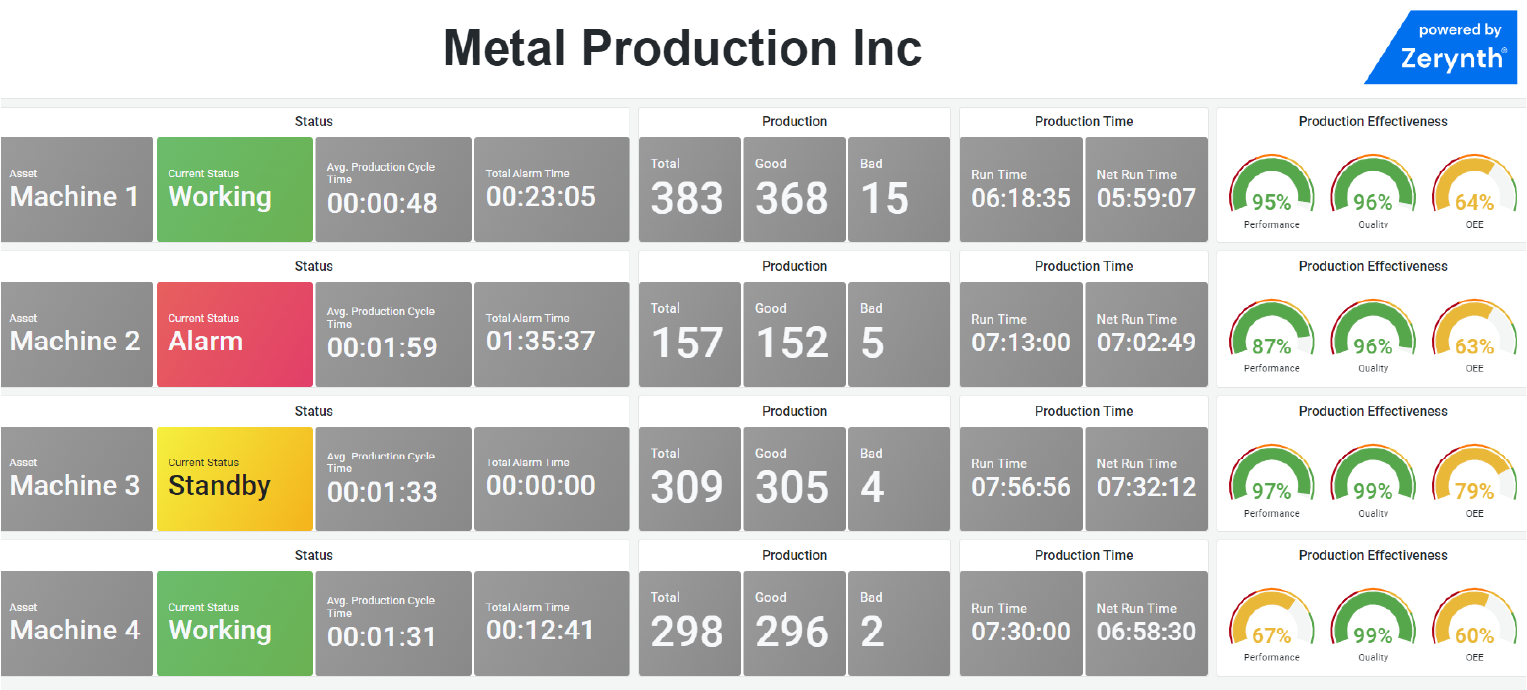
La Soluzione
La Zerynth IoT Platform è stata installata su ciascun macchinario presente nello stabilimento. Il parco macchine dell’azienda era composto da 35 macchinari sia di tipologia brownfield che greenfield, per cui è stato possibile estrarre i dati in retrofitting, attraverso il collegamento di una pinza amperometrica con ciascun edge device utilizzato. Tramite il valore di corrente, viene stimato il consumo energetico della macchina, da cui poi vengono derivate le ore di lavoro totali.
Avere a disposizione un sistema digitalizzato di monitoraggio dei macchinari, utilizzati per le lavorazioni meccaniche, ha permesso di rilevare processi non ottimizzati e di effettuare cambiamenti strategici per una riduzione dei tempi di attrezzaggio dei macchinari stessi.
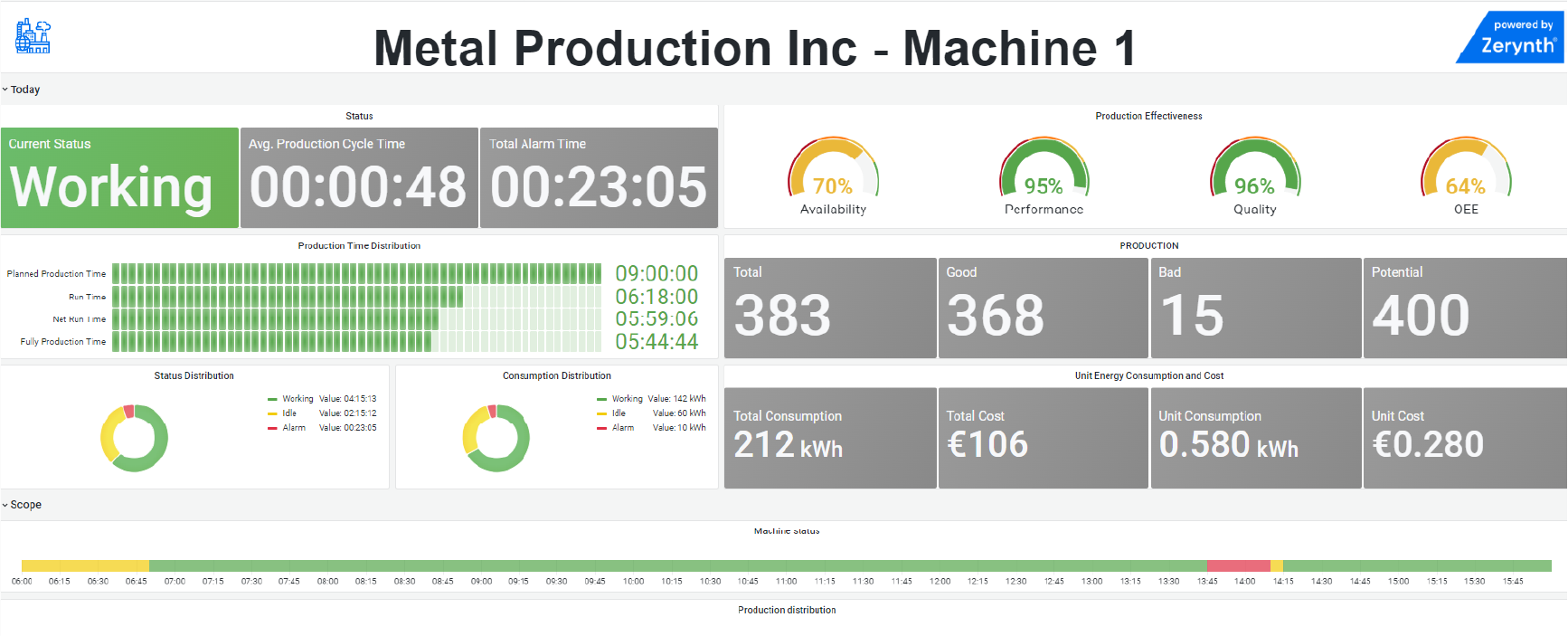
Scarica il case study per scoprire in che modo è ora possibile per l’azienda individuare le anomalie in modo immediato, ridurre sensibilmente i tempi di fermo macchina ed ottenere un’ottimizzazione completa del processo produttivo.
SETTORE:
Azienda del settore metalmeccanico
ASSET:
CNC, torni e frese
RISULTATI:
Ottimizzazione produzione
24/7 monitoraggio da remoto e riduzione tempi di attrezzaggio
Riduzione consumi energetici
24/7 analisi consumi e ore di lavoro dei macchinari
Diminuzione fermi macchina
100% rilevamento precoce delle anomalie
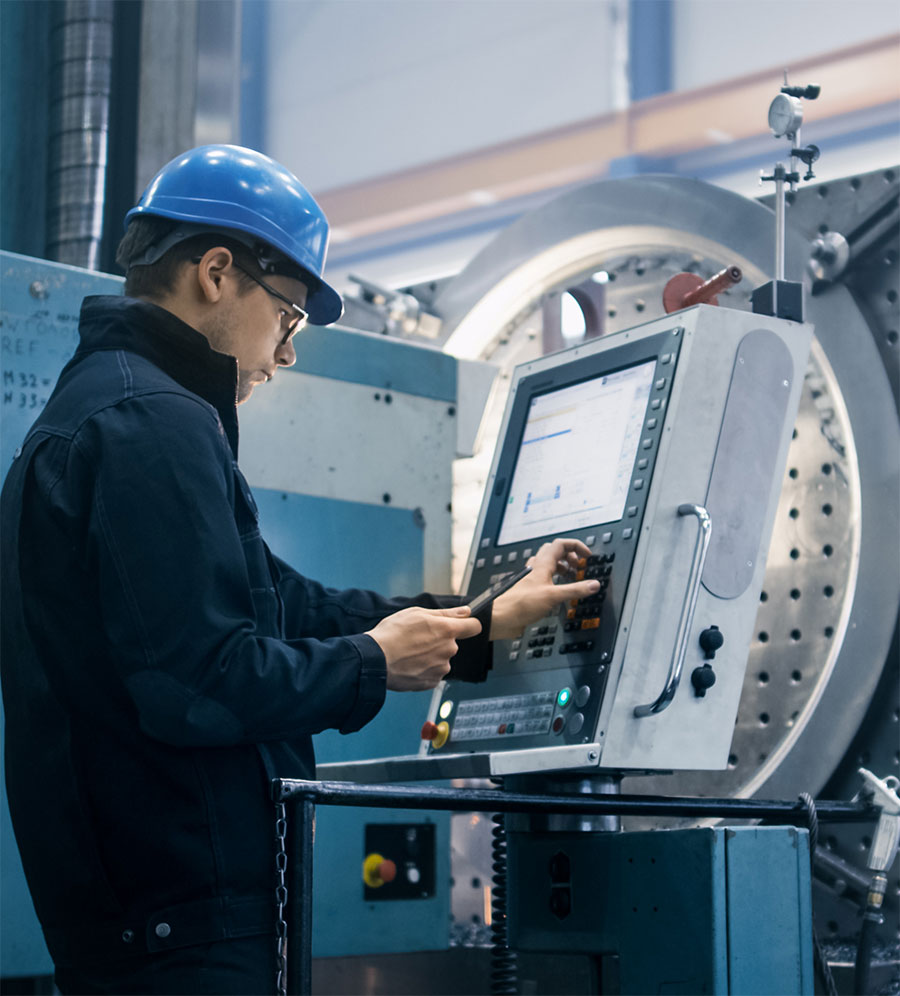
INIZIA CON ZERYNTH
Pronto a vedere cosa può fare Zerynth per la tua attività?